About Breaking
Our expertise leads to clean processes and higher yield
Clean breaking or cleaving with minimal loss requires extensive understanding of materials, methods and applications.
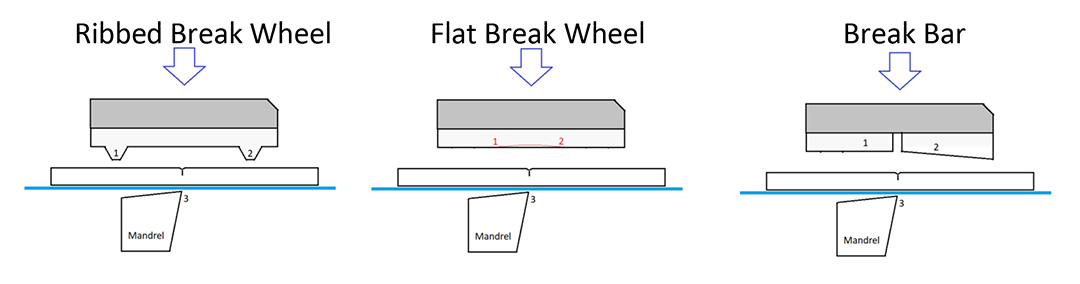
Loomis Industries uses two types of breaking devices: the break wheel, and the break bar (or break beam). The break wheels are either flat or “profiled”, where ribs are formed on the surface to press on the wafer at specific spacing. This allows us to limit the contact on the wafer to two or three narrow stripes as the wheel rolls across the wafer. When used correctly, this allows the user to avoid touching fragile structures on the surface of the die. The ribs can also be used to maximize leverage when working with thicker material. All three use the same three-point bend concept to break the wafer.
Two of the three beam-bending points come from a break wheel. The third point is provided by the wedge-shaped mandrel. The shape of the mandrel also limits the bending angle and therefore the strain that is applied to the wafer.
Die Separation. With the Loomis Machine, the results of your scribing and dicing are instantly observable. After a scribe line is broken, the dicing film under the wafer pulls the newly formed piece away from the body of the wafer forming a small gap that can be seen on the video screen.
Types of Breaking
Full Contact Dicing
Why use full contact dicing? When devices on a wafer are not sensitive to surface contact, a full contact process is easier to implement and maintain, as fewer alignments are needed on the break system.
Process: Full contact dicing is achieved by making a scribe line along the separation channels of a wafer and then applying a bending force across the scribe line. The scribe line creates a stress concentration that drives crack propagation down through the wafer. If the scribe line is created properly, the crack will propagate along the scribe line.
Applications: Detectors, optical filters, light emitting diodes, lasers
Limited Contact Dicing
Why use limited contact dicing? When the features on a device are very fragile, it is necessary to employ limited contact dicing rather than full contact dicing. The LSD-155Lt and LSD-155 dicing machines have breaking mechanisms that are compatible with our limited contact profiled break wheels.
Process: Limited contact dicing is achieved by making a scribe line along the separation channels of a wafer and then applying a bending force across the scribe line. The scribe line creates a stress concentration, creating a crack under the scribe line. If the scribe line is created properly, the breaking force will propagate that crack along the scribe line.
Applications: Edge-emitting lasers, modulators, vertical-cavity surface-emitting lasers (VCSELs), Micro-electromechanical systems (MEMS), MMIC’s with Airbridges, thick wafers
Cleaving
What is cleaving? Cleaving is the process of separating a material along its natural crystal planes.
Why cleave materials? Separation along natural planes creates the cleanest edge possible due to the regularity of the materials molecular structure. For semiconductor lasers, cleaved surfaces produce smooth mirrored surfaces, required for the proper function of the lasers.
Process: Cleaving is achieved by making a small notch, or peck (both are types of scribe lines) over the edge of a wafer, and parallel to the desired mirror. Then tensile strain is applied lateral to the notch with the break wheel. When done properly, the crack will propagate along a single crystal plane – the path of least resistance.
Applications: Creating laser bars, modulators, wave guides, and performing failure analysis
Ready to Increase Production?
We take an active role in helping you define processes that maximize yield.